Construction
NEXUS Gas Transmission commits great care, thoughtful planning, stewardship and safe work practices to building our network of pipelines. Construction of a new pipeline can involve thousands of workers, tons of high-strength carbon steel pipe and hundreds of pieces of construction equipment. Every step is guided by professionals with years of experience in building natural gas pipelines that meet the highest industry and government standards for safety, environmental protection and operational reliability.
Great effort is taken to minimize disruption to landowners during the construction process. We carefully plan every step of the project so we can install the pipeline and restore the area to its previous use as efficiently as possible.
Pipeline construction is very similar to a moving assembly line, in which several specialized teams are each assigned to perform a single, specific task along small sections of the pipeline. Once each team completes its task, another team follows closely behind to complete the next stage of construction. Once the entire process is completed for each section of the pipeline, the entire process is repeated again for the next section.
Below is a step-by-step guide illustrating each stage in the construction process.
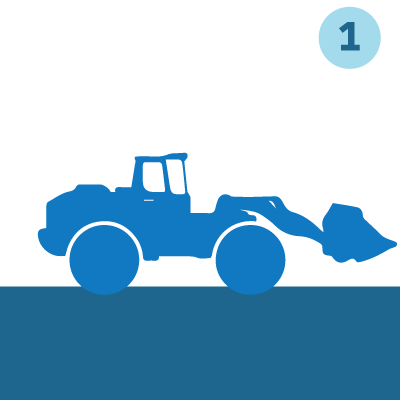
Clearing & Grading
Trees, brush and vegetation are cleared from the right of way, and the land is graded to meet the design specifications of the pipeline. Topsoil is then removed and placed in a protected area of the work site before additional subsoil is removed and stockpiled.
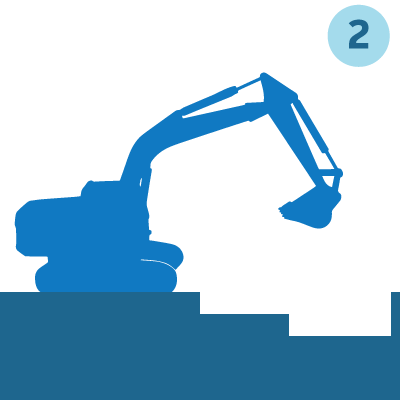
Trenching
A backhoe or trenching machine excavates a trench approximately 7 to 10 feet deep, and the excavated soil is temporarily stored alongside the trench.
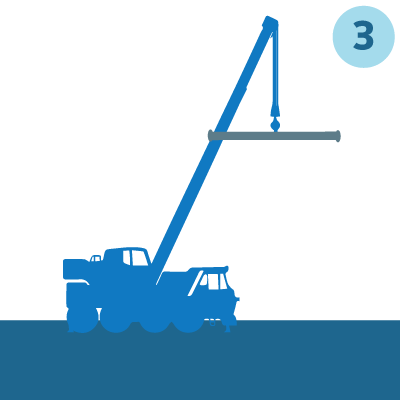
Stringing & Bending
Individual 40-foot joints of the pipe are transported to the work site and situated along the trench. A pipe-bending machine is then used to bend individual joints of the pipe to conform to the contours of the terrain and allow for directional changes in the pipeline.
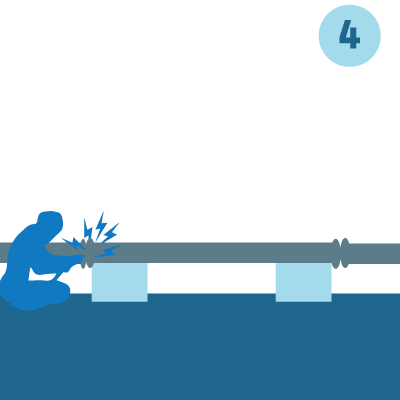
Welding & Inspection
After the individual pipe joints are bent to fit the trench, they are welded together by highly-trained, qualified welders. Each weld made on the pipeline is visually inspected and radiographs or ultrasonic images are processed on-site to ensure the integrity of every weld.

Coating
After weld inspection is complete, specialized epoxy coating is applied to each of the weld joint areas to prevent corrosion and other physical damage. The coating for the entire pipe section is electronically inspected.
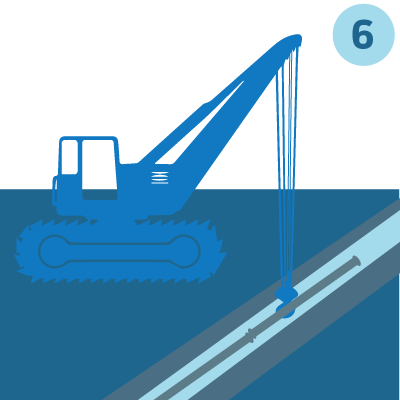
Depositing & Backfilling
Sections of the fully assembled pipe are deposited into the trench by mechanical equipment. The trench is then backfilled - first with subsoil and then with the segregated topsoil that has been stored in a protected area of the work site. Segregated topsoil is spread back over the construction work area and restored to its original profile.
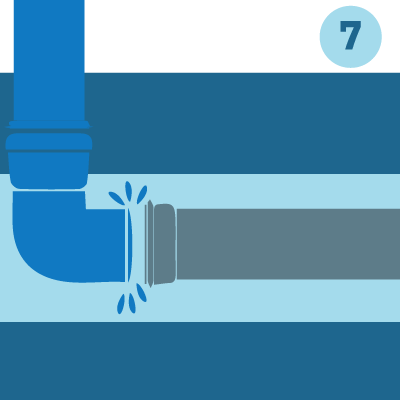
Hydrostatic Testing
As various pipeline sections are completed and backfilled, they are filled with water and pressurized to a point higher than the maximum pressure at which the pipe will ever be operated. This test pressure is held for a minimum of eight continuous hours to confirm the integrity of the pipeline.
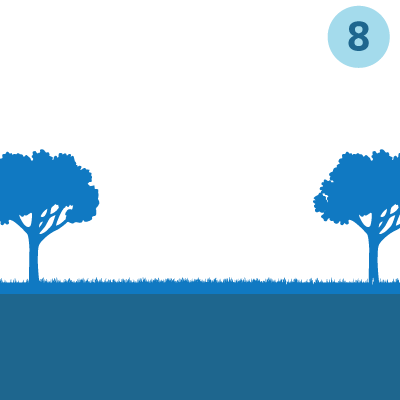
Restoration
Restoration begins as soon as the pipe is backfilled and continues until the construction work area is fully restored as close as possible to its original state. Topsoil and subsoil is regularly tested for compaction in agricultural areas disturbed by construction activities. Temporary workspaces will be allowed to return to their previous state. NEXUS recognizes and understands the integral part that drain tile systems play in many agricultural operations and will work diligently to minimize impacts and to restore all tile systems that may be disturbed during construction.